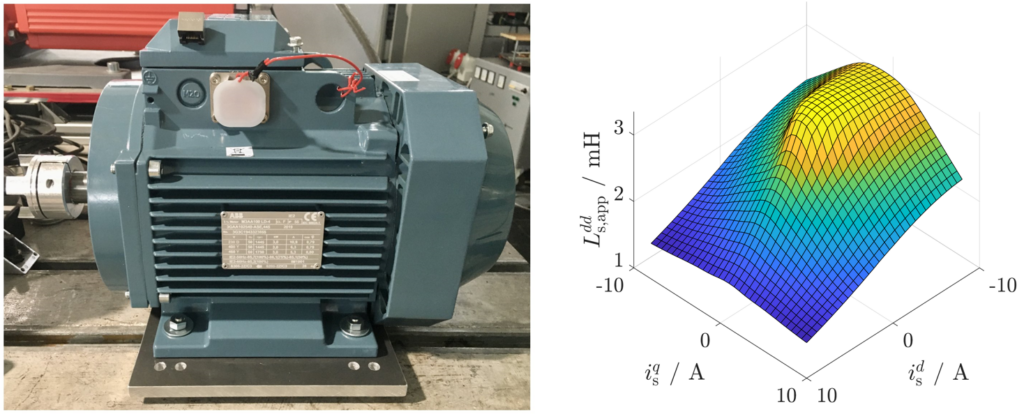
This project is funded by AVL SET GmbH.
Problem statement
Many control approaches for electrical drive systems that aim at improving dynamical behaviour, efficiency, robustness and fault-tolerance of electric drives are based on nonlinear electrical machine models. These models rely on precise knowledge of machine parameters and maps such as resistances, apparent and differentiable inductances and permanent magnet flux linkages.
These machine parameters and maps depend (nonlinearly) on all machine states, including currents or flux linkages, temperatures, rotor angle and speed due to physical effects such as magnetic saturation, cross-coupling and iron losses.
Methods and algorithms designed for machine identification estimate these parameters and maps based on static or dynamic tests. The accuracy of these estimated parameters and maps is significantly influenced by the quantity and quality of the measured machine data.
On the one hand, the use of several sensors to measure all machine states allows for a precise machine identification. On the other hand, there is also the need to identify machines in applications where only a few measured machine states (e.g. only stator currents) are available. Finally, a machine identification within a few seconds or a fraction of a second would be most attractive.
Project description
In this project, innovative algorithms for fast, precise, and simple but automated identification of electrical machines are to be developed, implemented, and validated which finally e.g. allow for rapid self-commissioning of electrical drives in general. The aimed-at objective is to identify machine parameters and maps with the highest possible accuracy from the smallest possible number of measured states within the shortest possible time.